- Product Knowledge
Explosion Proof Lighting: Essential Protection for Hazardous Environments
Industrial settings involving flammable gases, vapors, dusts, or combustible fibers demand specialized safety equipment. Explosion proof lighting isn’t just durable illumination; it’s a critical engineering solution designed to prevent catastrophic ignition within classified hazardous locations. Understanding its design, function, and proper application is non-negotiable for operational safety.
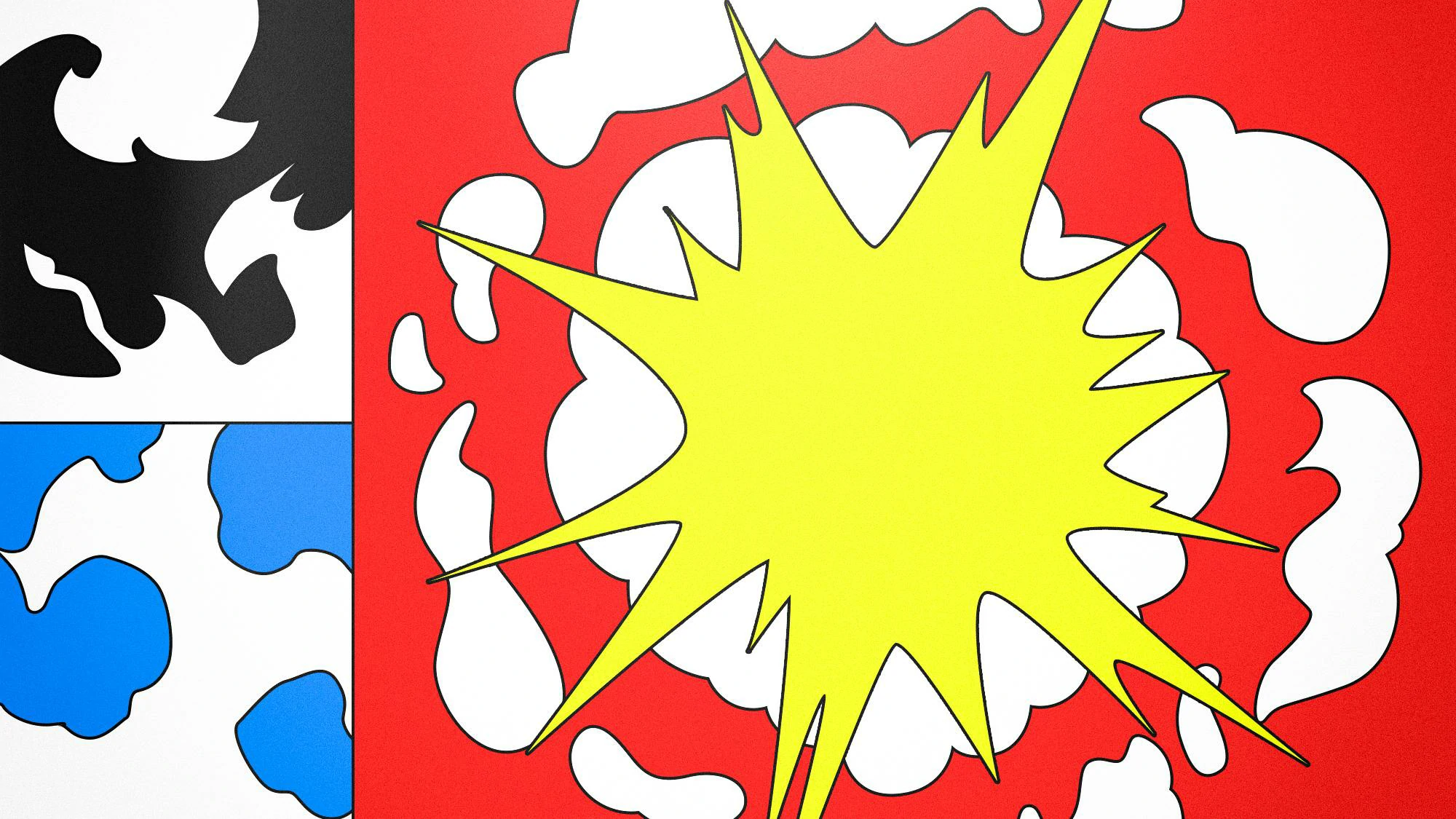
Why Standard Lighting Fails in Hazardous Areas
Ordinary light fixtures pose multiple ignition risks. Electrical arcing during switch operation, component failure generating sparks, or even the surface temperature of the bulb itself can act as an ignition source. Flammable vapor-air mixtures or combustible dust clouds require minimal energy to ignite. Standard fixtures lack the safeguards to contain such events or prevent surface temperatures from reaching dangerous levels.
The Engineering Behind Explosion Proof Fixtures
True explosion proof lighting relies on fundamental containment principles. Key design elements include:
Robust Enclosures: Fixtures use exceptionally durable materials like heavy-gauge aluminum, stainless steel, or robust polymers. These enclosures withstand immense internal pressure generated if an explosion occurs inside the fixture itself.
Flame Paths: Critical junctions (like between the housing and lens, or cable entry points) are machined to ultra-precise tolerances. Should an internal explosion occur, escaping hot gases and flames are forced through these long, narrow, cooled paths. This cools the gases below the ignition temperature of the surrounding atmosphere before they exit.
Temperature Control: Thermal management is paramount. Fixtures limit the external surface temperature (T-rating) to stay safely below the auto-ignition point of specific gases or dusts present. Designs incorporate heat sinks and carefully manage wattage. LED technology is dominant due to its inherently cooler operation.
Sealing: Gaskets and seals prevent flammable dusts or gases from penetrating the enclosure internally where electrical components could ignite them. This also protects against environmental ingress (IP ratings).
Spark-Free Components: Internal wiring and components are secured to prevent arcing or sparking, even under fault conditions. Special connections and switches are used.
Hazardous Location Classifications Dictate Fixture Requirements
Fixtures must be certified for the specific zone where they are installed. Systems like NEC (US/Canda – Classes, Divisions, Groups) and ATEX/IECEx (Global – Zones, Gas Groups, Temperature Classes) define environments based on:
Material Type: Flammable Gas/Vapor (Group IIC, IIB, IIA), Combustible Dust (Group IIIA, IIIB, IIIC).
Presence Probability: Division 1 (Hazard present continuously/intermittently) vs. Division 2 (Hazard present abnormally); or Zone 0/1/20/21 (high probability) vs. Zone 2/22 (low probability).
Ignition Temperature (T-Rating): Fixtures are marked (e.g., T3, T4, T6) indicating their maximum safe surface temperature.
Applications Demanding Explosion Proof Lighting
These lights are vital across numerous high-risk industries:
Oil & Gas: Refineries, drilling rigs, pipelines, processing plants.
Chemical & Pharmaceutical: Manufacturing plants, solvent storage, labs.
Mining: Coal mines (methane risk), grain handling, metal processing.
Paint & Coatings: Spray booths, mixing rooms.
Wastewater Treatment: Digester tanks, pump stations.
Aerospace: Fueling areas, hangars.
Grain Silos & Food Processing: Combustible dust environments.
Advantages of Modern Explosion Proof LED Lighting
LEDs have revolutionized this sector:
Lower Surface Temperatures: Significantly reduced heat output simplifies meeting T-rating requirements.
Energy Efficiency: Drastically cuts operational costs compared to traditional HID fixtures.
Long Lifespan: Reduces maintenance frequency in hard-to-access or hazardous zones.
Durability: Solid-state design withstands vibration better.
Instant On/Off: No warm-up time; suitable for areas requiring frequent switching.
Improved Light Quality: Better color rendering and light distribution.
Installation and Maintenance: Non-Negotiable Compliance
Proper installation by certified electricians following the fixture’s certification and relevant codes (NEC, IEC) is mandatory. Regular inspection and maintenance are crucial to ensure seals remain intact, lenses are undamaged, and corrosion hasn’t compromised flame paths or structural integrity. Never modify certified fixtures.
Conclusion
Explosion proof lighting is engineered safety. It prevents electrical equipment from becoming the source of disaster in volatile environments. Selecting fixtures with the correct certifications for the specific hazardous location classification, leveraging the benefits of modern LED technology, and adhering to strict installation and maintenance protocols are fundamental responsibilities for ensuring worker safety and facility protection in these critical industries. Never compromise on specification or compliance.